LFP batteries are improved, cheaper battery tech
There’s been a lot of buzz lately about the next big innovation in electric vehicle battery technology: LFPs. Lithium ion phosphate batteries are highly stable, have a long life, and are more resistant to heat damage than their lithium nickel cobalt aluminum oxide (NCA) and lithium nickel manganese cobalt oxide (NMC) cousins.
NCAs were the first batteries to be used in electric vehicles. They can charge rapidly and have higher energy density than LFPs, meaning they can hold more power and range in less space. That’s partly why NCAs and NMCs are still the most commonly used batteries for EVs. But that’s beginning to change. Many automakers are switching to LFPs, including Tesla, Ford, and Rivian.
LFPs are durable. Studies show LFP batteries have a cycle life 2 to 4 times longer than NMC batteries. Recent technological advances, including the addition of manganese, have allowed LFPs to match the range of cobalt battery cells. Not only that, they’re less likely to experience thermal runaway and their materials are easier and cheaper to source, bringing down costs for automakers and consumers alike.
.webp)
Why OEMs are switching to LFP?
Pricing and availability are the most significant factors driving automakers’ embrace of LFPs. Nickel and cobalt prices have more than doubled since 2021. From extraction to production, battery minerals travel an average of 50,000 miles, meaning that natural disasters, international conflict, and even bad weather can all interrupt or delay shipments and deliveries.
And, conflict has been a cause of supply chain instability even in the past few years. A significant chunk of the world’s nickel is mined in Russia and most cobalt is mined in Congo, both countries with political and ethical baggage. LFP minerals can be obtained in North America, reducing transportation costs and securing the supply chain. Tesla CEO Elon Musk, in particular, has cited concerns about the nickel supply as a motivating factor in making the switch to LFPs. He’s called on mining companies to get more nickel, taking care to emphasize said mining should be done in an environmentally conscious way.
Bringing Down the Price
Setting aside the ethical and political motivations for a moment, the cost savings of LFP batteries are hugely appealing to automakers, always eager to increase their bottom line. LFPs are about 20% cheaper than other types of batteries. Currently, nickel is priced at about $18,000 per tonne and cobalt at about $33,000 per tonne. Meanwhile, iron ore costs about $120 per tonne. That’s significant savings.
When it comes to the actual EV batteries, NCA battery cells clock in at about $120.30 per kWh and NMC battery cells at about $112.70 per kWh. LFP battery cells? They only cost about $98.50 per kWh. While LFPs only account for 21% of the EV battery market today, by 2026 they’re expected to make up 38% of the EV battery market.
Switching to LFPs would reduce or eliminate the need to rely on nickel and cobalt. That means automakers would no longer need to work with mining operations with questionable morals and business practices. (At least, for those materials. lithium mining has its own issues.) A move away from nickel and cobalt would also make it easier for American companies to participate in a domestic supply chain secure from foreign influence. Though they still have an environmental impact, LFP cells produce on average 15-25% lower carbon emissions than NMCs. In a swiftly heating world, every reduction in carbon emissions counts.
With all their benefits, it’s no wonder we’ll soon be seeing more EVs with LFPs under the hood.
The Problem with Cobalt and Nickel
Cost savings are great, but there are other reasons to switch away from cobalt and nickel based batteries. In fact, the reality of battery mineral mining is a far cry from the lofty ideals of the clean energy revolution. The auto industry’s reliance on nickel and cobalt has led companies to look the other way when it comes to environmental and human rights abuses. Brief mentions of these less than savory business practices pop up from time to time in the conversation around battery production, but it’s worth getting into the specifics.
Tesla, for example, gets its nickel and cobalt from Glencore, a mining company with no less than 70 allegations of human rights abuses against it. About 70% of the world’s cobalt comes from the Democratic Republic of Congo, where tens of thousands of children work up to 12 hours a day in dangerous mines and often make only $3.50 a day. Entire communities have been destroyed when mining operations seized their mineral-rich lands and workers are encouraged not to report injuries that would lead to incriminating safety reports. Four of the top five cobalt mining companies have human rights allegations against them.
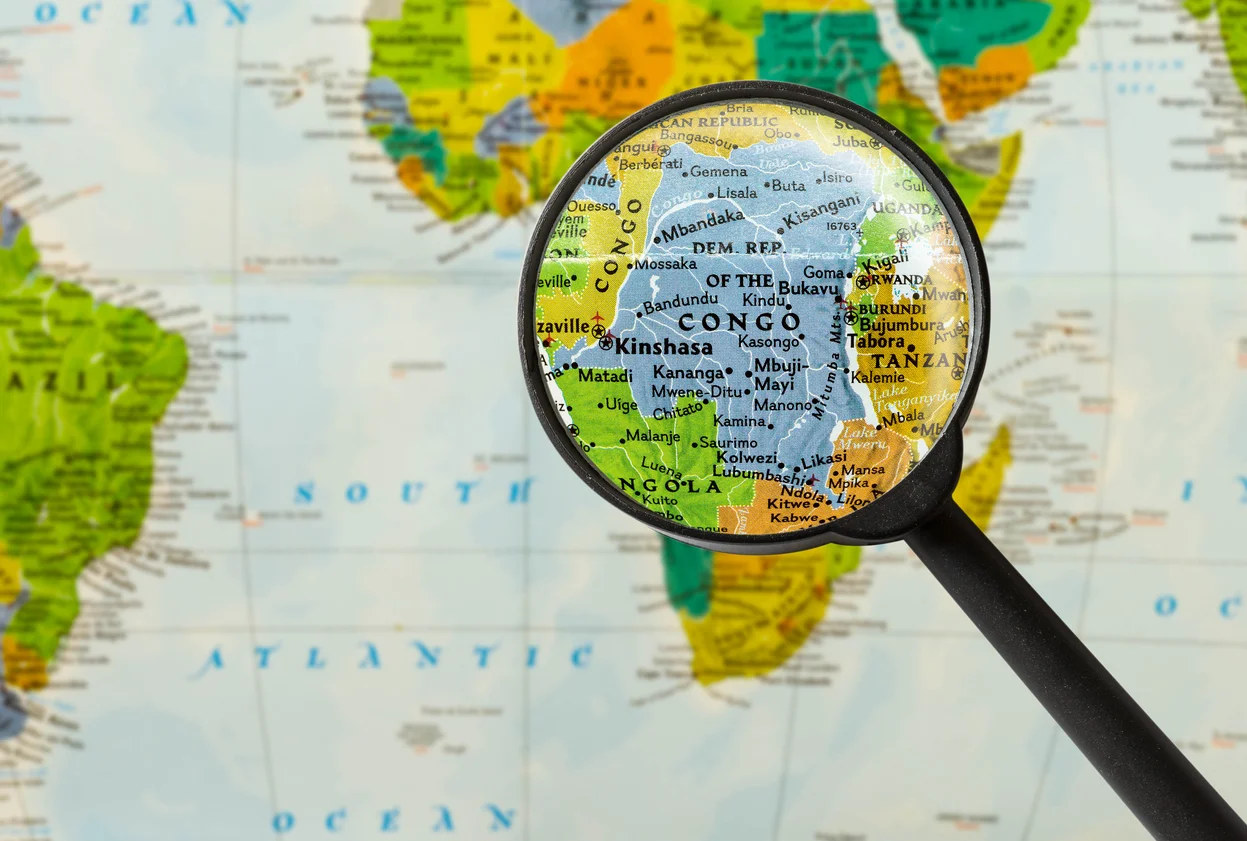
Nickel mining isn’t any better. Three of the top five nickel mining companies have human rights allegations against them. Nickel mining operations in Russia produce some of the worst air pollution in the world. Rainforests in Indonesia have undergone extreme environmental degradation and deforestation due to the horizontal surface mining used to harvest nickel.
Amnesty International has long called for leaders in the electric vehicle industry to make sure their batteries are ethical, but most automakers don’t really know where their supplies come from. Though they are working to improve supply chain transparency, the risk of harm from these mining operations is still high. Switching away from cobalt and nickel battery chemistries may be the best solution.
Security and Supply
There are also geopolitical complications with EV battery production. American efforts to control the EV battery supply chain are hampered by the fact that most clean energy metals are produced and refined in other countries, many of which are not friendly trade partners. China owns some of the largest cobalt mines in Congo and is the biggest processor of virtually all clean energy metals, controlling over 80% of global raw material refining capacity. The Biden administration has already warned China could use its control of cobalt to derail American electric vehicle manufacturing.
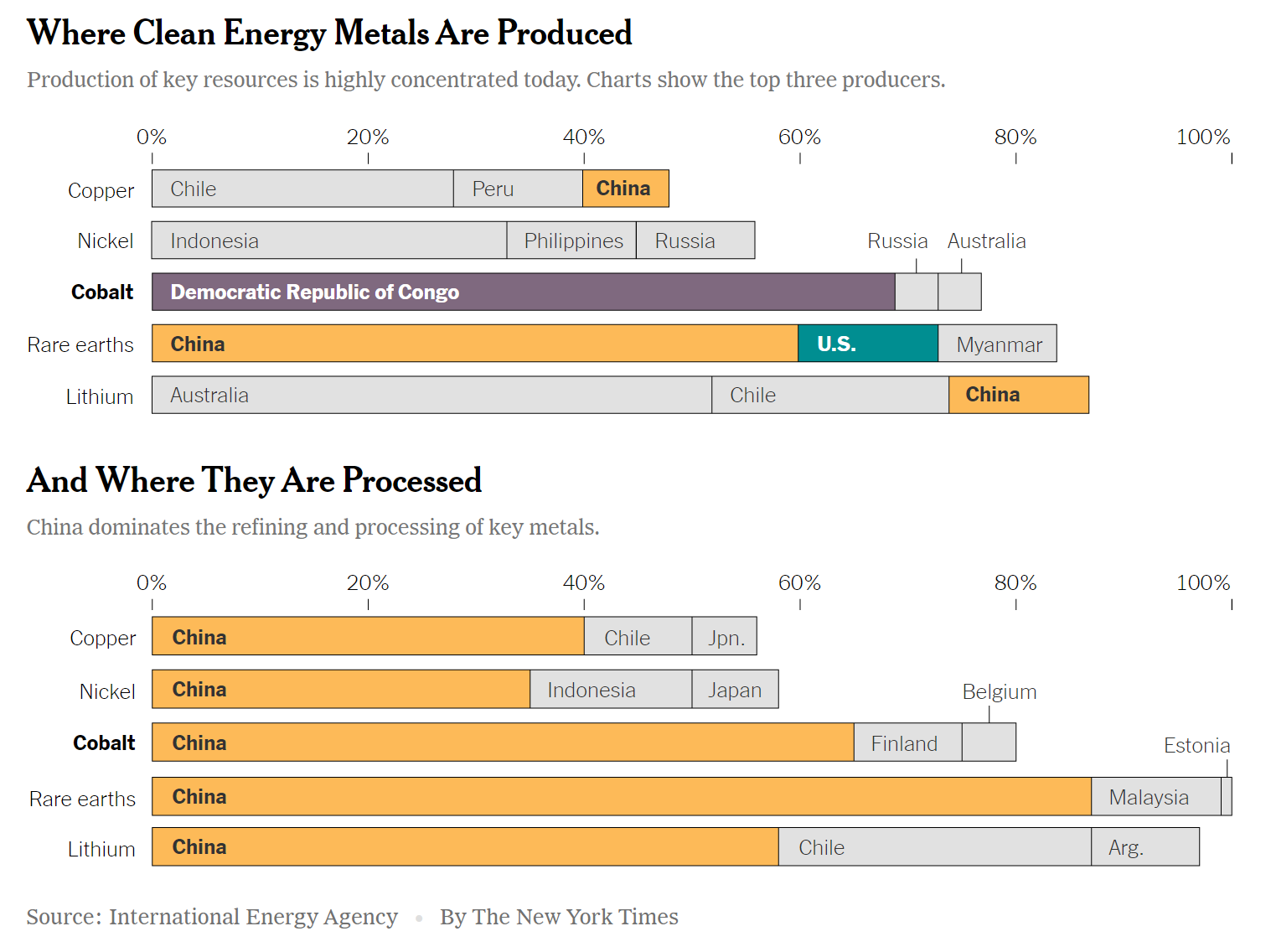
The U.S. has a plan to establish a secure, domestic supply chain for EV batteries. Already the EV manufacturing sector is booming. Switching to LFPs is one strategy to escape the need for internationally sourced cobalt and nickel.
Batteries: The Lesser Evil?
Lobbyists and other friends of the fossil fuel industry may try to use the environmental and ethical concerns of mining as an argument against the switch to clean energy, but it’s important to remember the oil and gas industry is also riddled with abuse.
Residents of oil and gas field communities have experienced negative health effects including respiratory problems, headaches, nausea, miscarriages, and cancers. Air pollution from fossil fuel combustion causes 12,000 premature deaths worldwide every day.
Hydraulic fracking, which uses high-pressure fluid injections to extract natural gas from rock formations, consumes billions of gallons of water that are then tainted with toxic chemicals and injected back into the earth in gigantic wastewater pits. In addition to potentially poisoning local drinking water, the injection of wastewater can cause damaging earthquakes.
Fracking destroys plant and animal habitats, leading to a loss of biodiversity. There’s also the impact on climate. The oil and gas industry is a primary driver of climate change. Fossil fuel combustion is responsible for 73% of U.S. greenhouse gas emissions.
Though battery material mining has many problems, the oil and gas industry is worse. As Mark Dummett, a researcher at Amnesty International, said after the U.S. added lithium-ion batteries to a list of goods known to be produced with child labor,
“There is a danger with this labeling that it demonizes the EV industry, the battery industry. Anyone worried about the state of the planet should be alarmed by that.”