This article talks about the common battery pack configurations found in EVs
Cells Inside Modules Inside Packs
There are three levels to an electric car battery. The smallest is the battery cell, which is a singular, closed loop system that converts chemical energy to electrical energy and back again. A battery cell has a few major components: electrodes (the anode and cathode) and their respective charge collectors (one positive, one negative), an electrolyte that the lithium ions flow through to generate electricity or recharge, and an external casing.
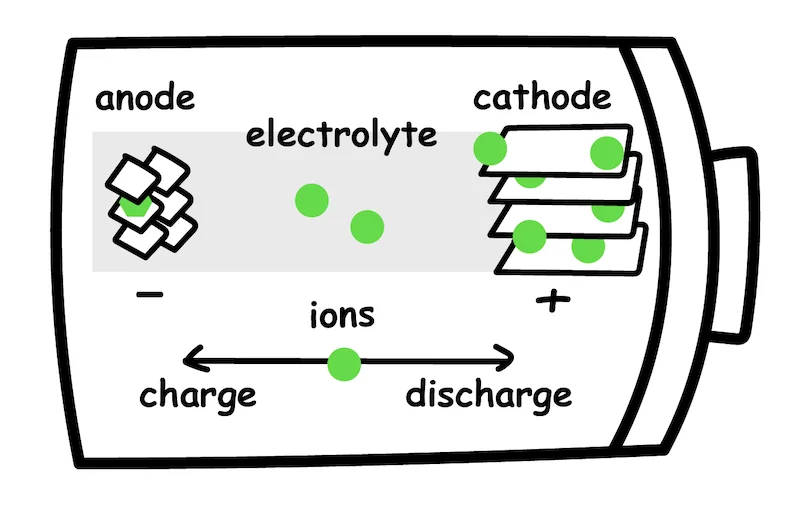
The battery discharges and produces electricity when the lithium ions move from the negative terminal to the positive terminal. When you plug in a battery to charge it, the ions move in the opposite direction, from the positive terminal to the negative terminal. It’s important to remember this is a physical process. Lithium ions are very small, but they are physically traveling back and forth through the battery. This movement contributes to battery degradation over time.
To get more power, you need more battery cells. Individual battery cells can be grouped together into battery modules, which are just a configuration of many single cells. The battery modules can be grouped together into battery packs, which are modules combined with thermal and battery management software and hardware.
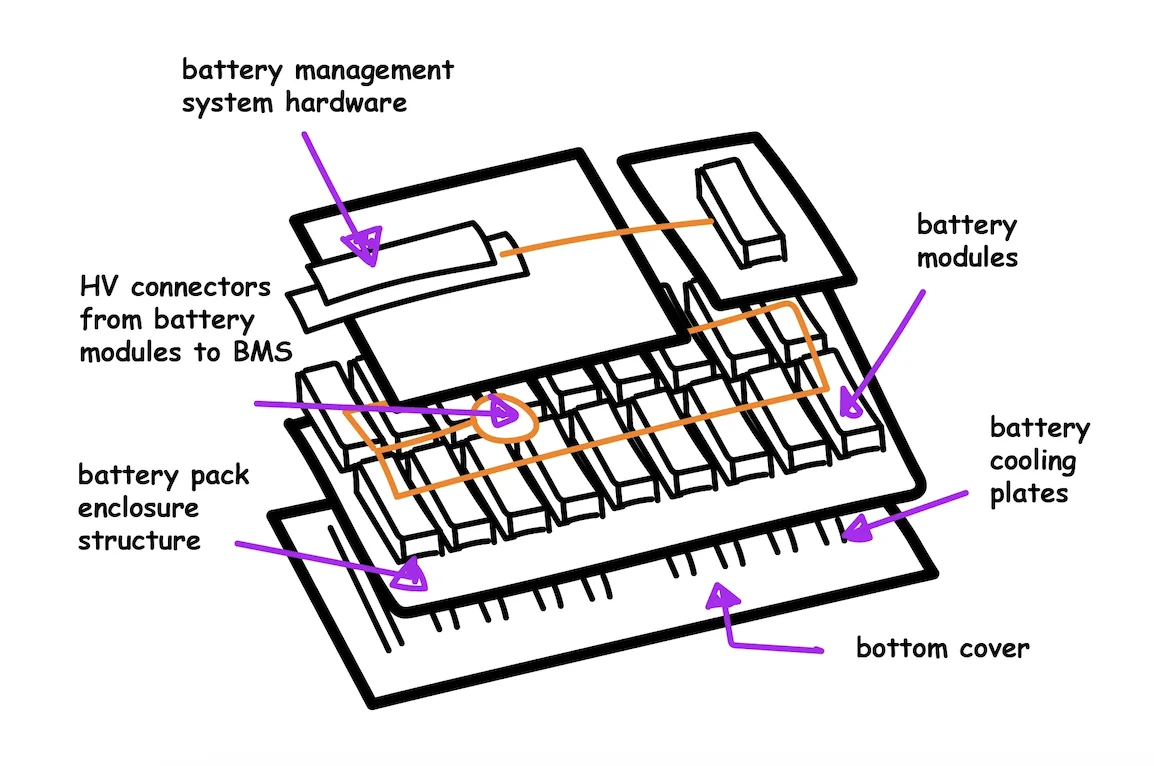
All these cells and modules need to be arranged somehow, ideally in an efficient way that will prevent the battery cells from overheating. This is where the different battery configurations come into play.
Cylindrical Cells
As you might guess from the name, the battery components of cylindrical cells are all rolled up neatly into a cylinder. They look a lot like the AA batteries you have at home. Cylindrical cells were one of the first mass-produced types of batteries and they are still well-suited for automated manufacturing.
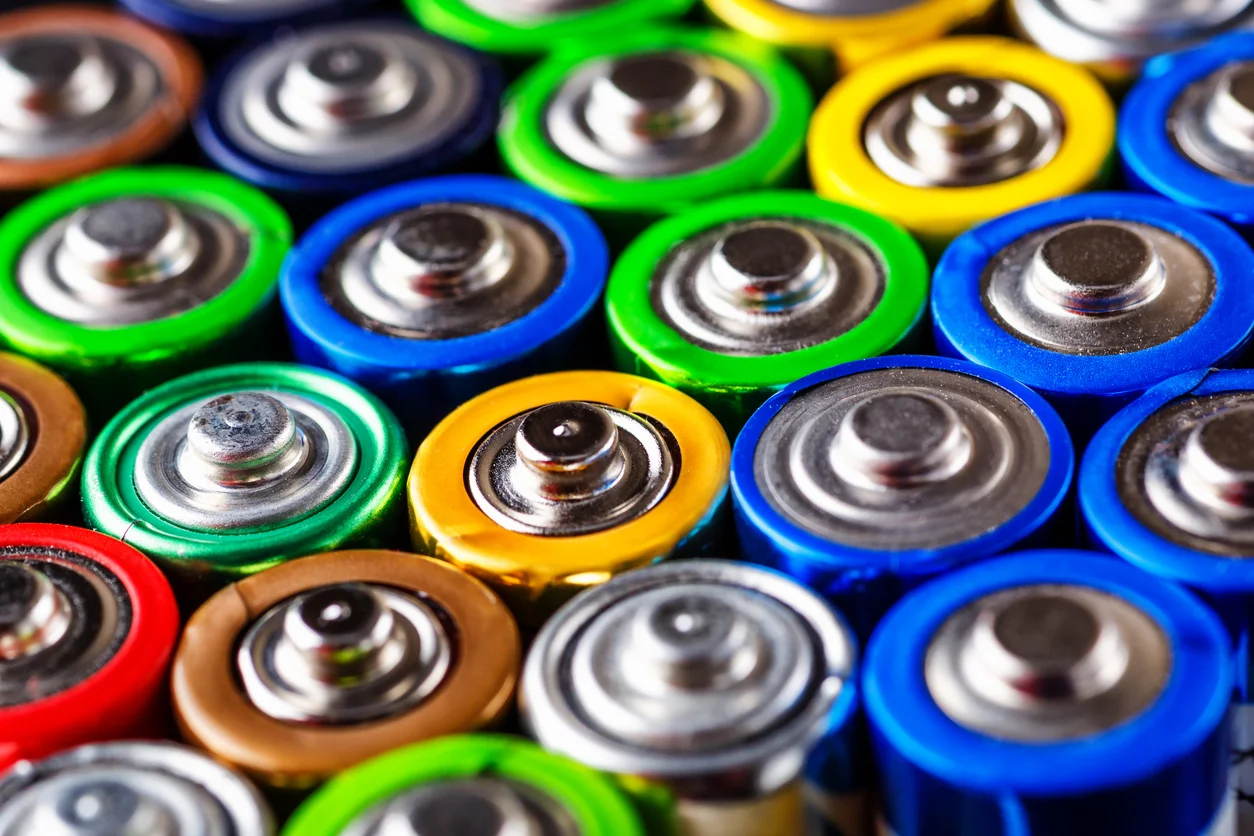
Pros: Cylindrical cells have a tight metal case that helps prevent breaking and leakage. The cells are mechanically stable, evenly distributing internal pressure across the cell circumference, allowing it to tolerate more pressure without deformation. They also have high temperature resistance and better thermal management. It’s easier for coolant to move through the spaces between the cells in a battery pack.
Cons: On the downside, because of their cylindrical shape, the gap between cells can be relatively large, meaning the packs take up more space. The metal casings are also heavier than other casing options, which can be something of a disadvantage for moving vehicles.
Prismatic Cells
The battery components of prismatic cells are laid out in sheets and sandwiched together, sort of like a stack of paper that’s been folded over and squeezed into an envelope. The envelope, in this case, is a metal or hard-plastic rectangular casing.
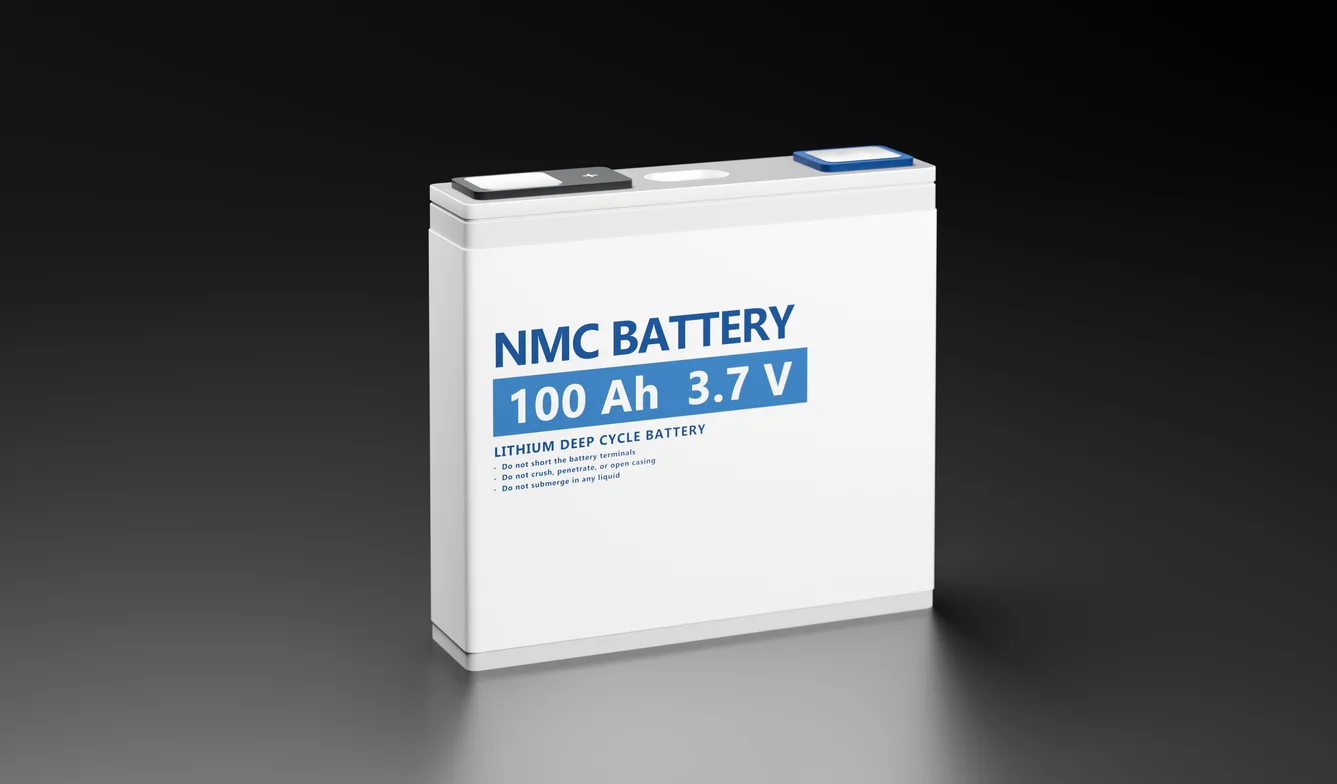
Pros: These battery cell boxes can be stacked neatly together, optimizing the use of available space. This allows for more flexibility in design of the packs.
Cons: Unfortunately, this organized stacking can make thermal management more difficult, as there is no space between the cells for cooling. The corners can also cause more stress to the battery components than cylindrical cells, and although they suffer less from swelling than pouch cells, they don’t do quite as well on that front as cylindrical cells.
Pouch Cells
Rather than being crammed into a rigid metal casing, pouch cells are sealed within minimalistic foil packaging. They look kind of like individually wrapped Pop-Tarts.
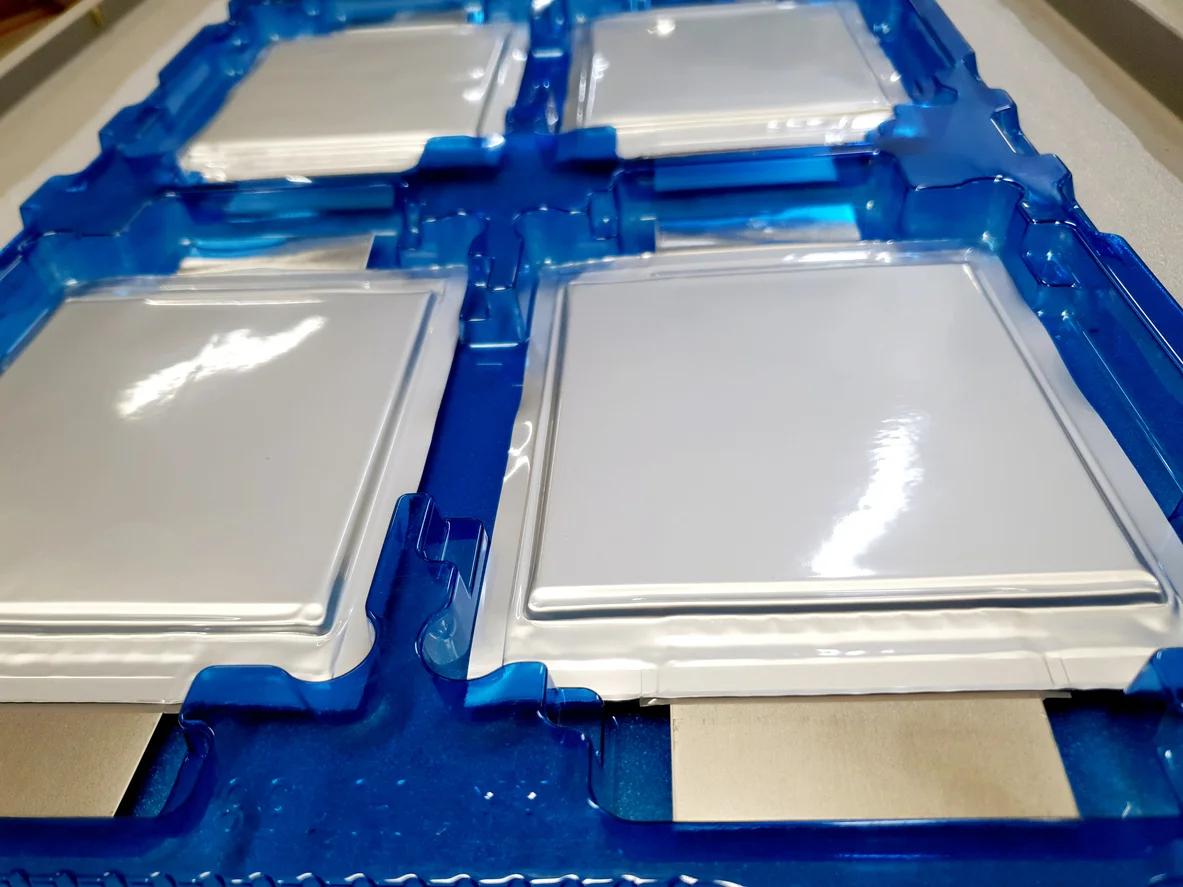
Pros: The lightweight foil creates flexible cells that can easily be arranged into small spaces and significantly reduces the overall weight of the battery pack. Pouch cells are safe and just as effective as cylindrical battery cells. They have low internal resistance (which means energy flows freely) while still packing a high power capacity.
Cons: Unfortunately, pouch cells are expensive to develop and produce. Because they are only protected by soft foil, pouch cells cannot be placed near sharp edges and they have a higher possibility of leakage than cells protected by hard metal shells. Also, although pouch cells won’t explode when there’s a problem, the pouches can swell, sometimes as much as 10%, inflating like a balloon.
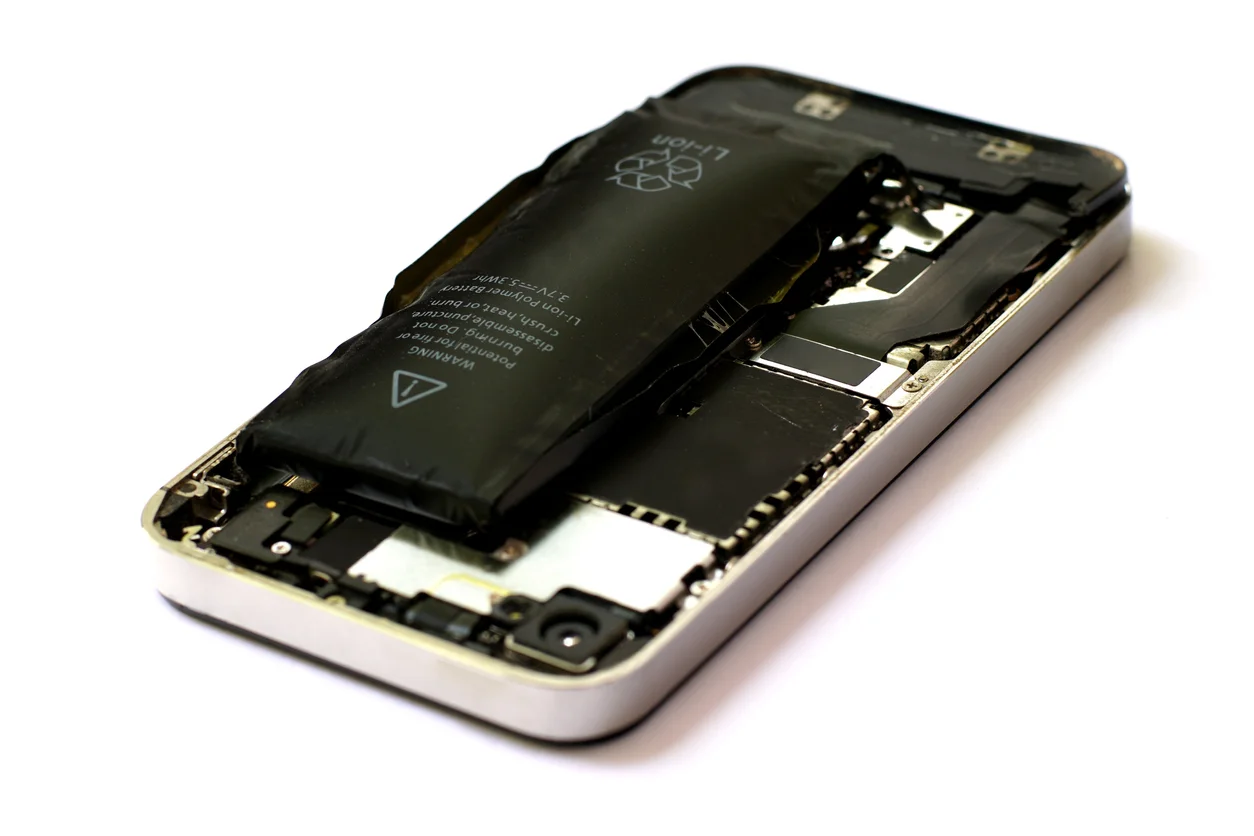
Battle of the Cells: Which Type is Better for EVs?
Cylindrical cells and pouch cells are both commonly used in electric vehicles, for different reasons. Cylindrical cells have good heat dispensation and high consistency in performance, whereas pouch cells have good cycle performance and safety while allowing for lightweight, flexible design. As for which type is better, EV manufacturers disagree.
Tesla, Rivian, and Lucid make EVs with excellent range and efficiency, and some attribute their success to the use of cylindrical cell batteries. In fact, Tesla has sworn off the use of pouch cells, citing concerns about fires and thermal runaway. Some companies, on the other hand, swear by pouch cells. Hyundai and Ford both use pouch cells in their vehicles. In addition to their customizable, lightweight designs, pouch cells might be the first step to an even better EV battery option: solid state. Though solid state EV batteries are not yet available on a commercial scale, solid state batteries can only be made with pouch cells, which may push more manufacturers to adopt them. GM favors large-format pouch cells, packing their vehicles with “the fewest number of the largest cells possible.”
However, recently rumors have surfaced indicating GM might be making the switch to cylindrical cell batteries, a big change for a company that has relied on pouch cells for over a decade. BMW is also embracing cylindrical cell batteries, anticipating performance enhancements for their new vehicles, like faster charging and longer range.
It’s impossible to predict which type of battery cell will win out in the end. As technology improves and evolves, new considerations will come into play, pushing design and manufacture in unanticipated directions. In all likelihood, cylindrical, prismatic, and pouch cell batteries will all have a place in the EVs of the future. Ultimately, it will be the needs and desires of drivers, and the limitations of production, that will push manufacturers to choose one cell type over another. As times change, the preferred cell type will change as well.
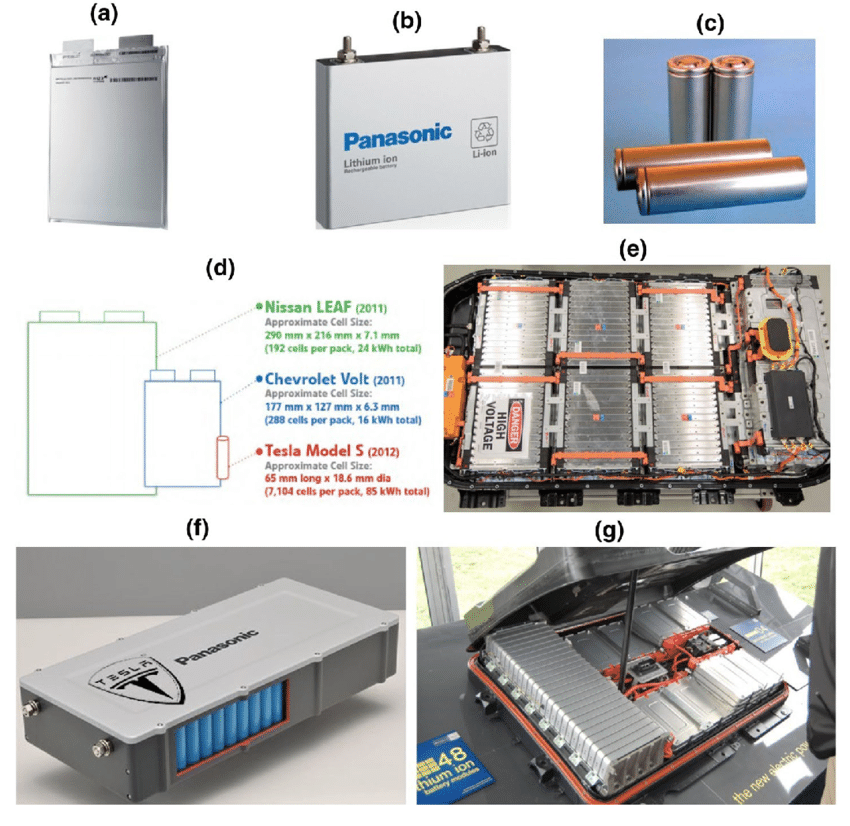
Written by River James, a writer, editor, and researcher based in San Diego, California. For her personal thoughts and musings, check out her Substack.